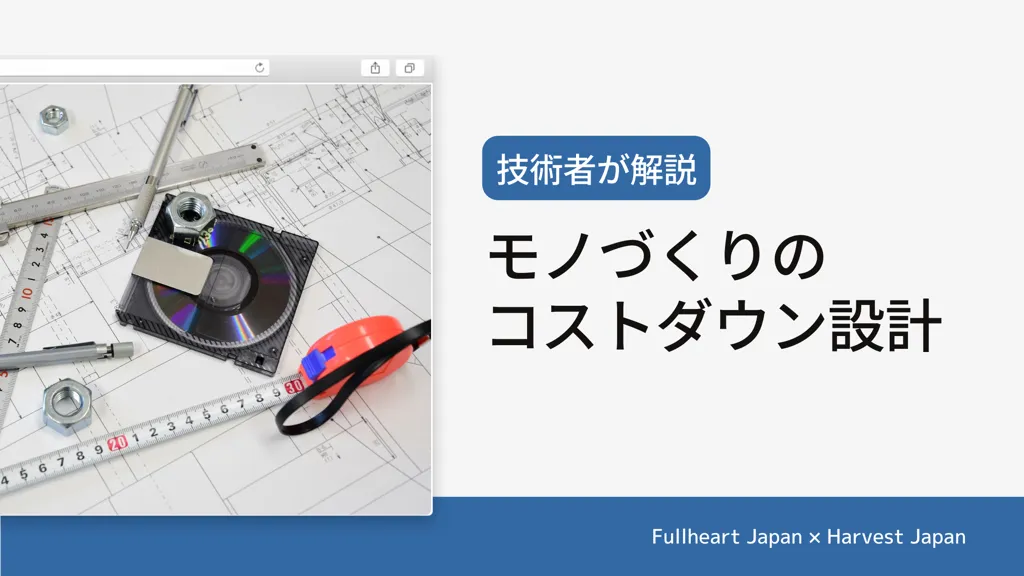
コストダウン設計とは、製品設計の段階で、コストを最小限に抑えながら、価値の最大化を目的とした設計手法のことです。VAとVEの2つの方法があり、それぞれの目的が異なるため、使い分けが重要です。
しかし、実際に細かく突き詰めると意外な落とし穴があったり、知見がなければ見落としてしまうコストダウンもあったりするのが実情です。そこで本記事では、コストダウン設計の内容や考え方、事例を紹介します。
コストダウン設計とは
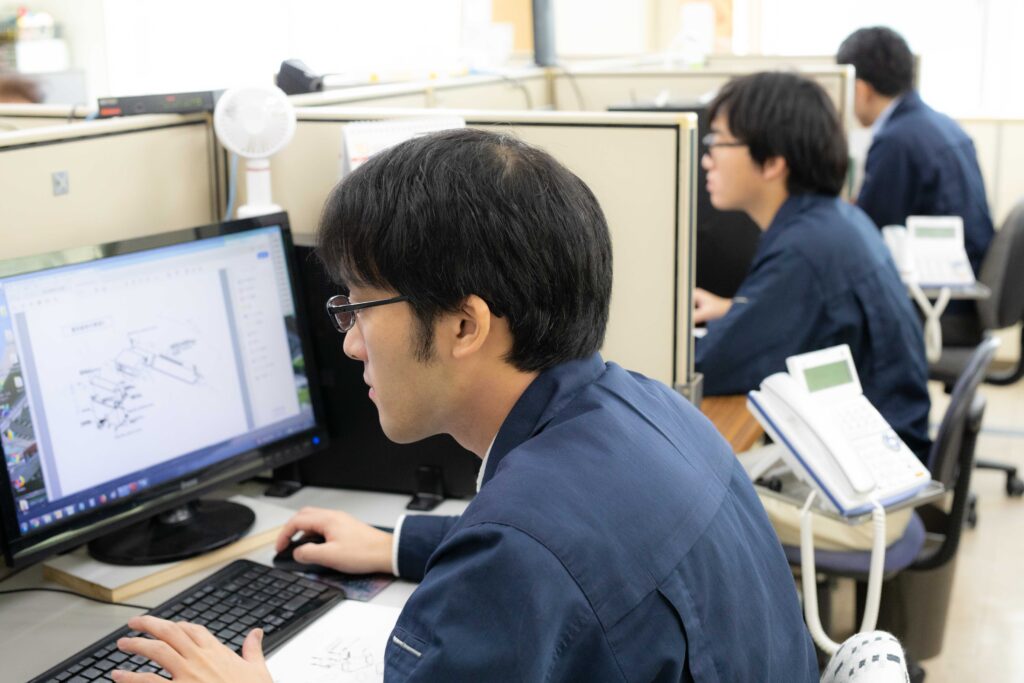
コストダウン設計とは、製品設計の段階で機能を高く維持しながら、コストを最小限に抑える設計手法のことです。フルハートジャパンでは、お客様の新規設備導入時にコストを抑える提案をさせていただき、この手法はVE(Value Engineering)と呼ばれます。
バリューエンジニアリングとは、顧客のニーズを把握し、製品やサービスの付加価値の最大化を指します。主に機能分析、代替案の検討、評価と実行の3つのステップで実施し、製品やサービスの品質を維持しながらコストを削減します。
その結果、品質や性能を維持しながら顧客が求める価値を提供し、競争力を高められるのが利点です。今後も、継続的に最新技術や最新の製品を活用し、付加価値を最大化していく必要があるでしょう。
コストダウン設計の目的
コストダウン設計の主な目的は、主に製品の設計段階でコスト削減を図ることです。単純に製品のコストを削減するだけに限らず、下記のような目的でも実施されます。
- 製品のコスト削減
- 競争力の向上
- 製品の改善
- リスクの回避
その上で重要なのは、設計段階における図面や仕様書で製品の約8割が決まってしまい、見直しできる項目が減ることを踏まえて、最初からムダを減らすことです。
コストダウン設計の重要性
コストダウン設計の重要性が高まる理由は、下記の3つが挙げられます。
- 市場競争力を高める
- 利益率を向上させる
- 新しい技術やアイデアを探求できる
顧客は、同じ品質や機能の製品やサービスであれば、より安い価格のものを選びます。したがって、コストダウン設計によって価格を下げることは、販売量やシェアを増やすことにつながります。
また、製品やサービスの原価を削減できれば、売上から差し引く経費を減らせることで利益率を高められ、企業の収益性や成長性を向上できるのも利点です。
そして、コストダウン設計には、既存の製品やサービスの改善だけでなく、新しい製品やサービスの開発も含まれます。そのため、顧客のニーズや市場の変化に応えるために、新しい技術やアイデアを探求できるでしょう。
このように、コストダウン設計は企業の経営戦略において必要不可欠なものとなり、持続的な成長と競争優位性を確保する手段としてその重要性を高めていると考えられます。
コストダウン設計に重要な3つの生産安定性の要素
コストダウン設計において、生産設計を見直すのに何からはじめれば良いのでしょうか。フルハートジャパンでは、コスト改善のために下記に挙げた3つのチェック項目を考えます。
安定性の項目 | 問題点 | 対策方法 |
---|---|---|
設備安定性 | 機械が止まったり、号機ごとに差があったりする | 設備機能を確認し、改善を行う |
品質安定性 | 不良やロスが生じている | 直行率の管理や設備の見直しを行う |
調達安定性 | 納入遅れや不良品の納品がある | 仕入先と協働し、短納期調達と小ロットでの納品を可能にする |
ここからは、具体的にコストダウンを実現する製造設計の進め方・方法を紹介します。
コストダウンを実現する製造設計の進め方・方法
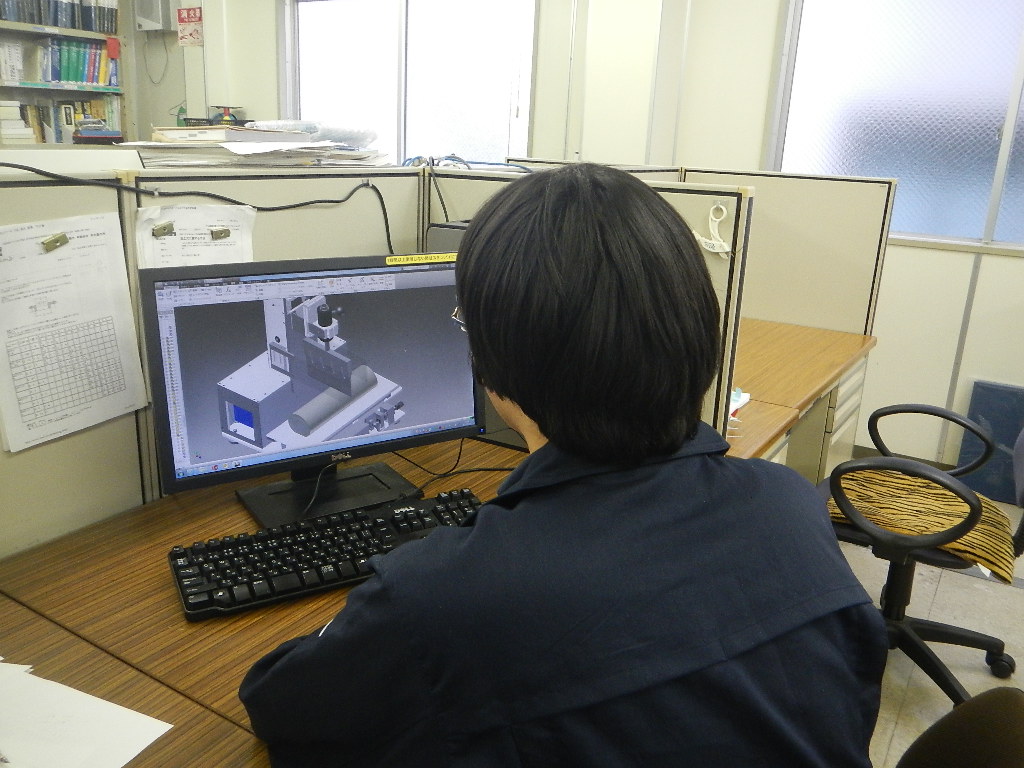
コストダウンを実現する製造設計の進め方・方法としては、DFM・DFAで効率よく無駄を省く手法があります。
DFM・DFAで効率良く無駄を省く
DFM・DFAという2つの設計手法を組みあわせることで、製品開発の効率性を高めることができます。
手法 | 略称 | 内容 |
Design For Manufacture | DFM | 設計初期段階で材料選択・部品構成・加工方法などの観点から見積もりを行って製造工程におけるコスト削減を目指す手法 |
Design For Assembly | DFA | 設計段階から組立流れを考慮した設計を行って組立性を向上させる手法 |
設計初期段階からコストを抑えられるDFM、組立容易性を考慮した設計を行うことで部品の無駄を省けるDFAの2つを組みあわせて、生産効率を高めることが大切です。
フルハートジャパンでは、DFM、DFAに加え、製品のテストを容易にするDFT(Design For Testability)の手法も採用、テスト用の端子を製品の前面に配置するなどの工夫により、お客様のコスト削減をサポートします。
コストダウン設計のポイント
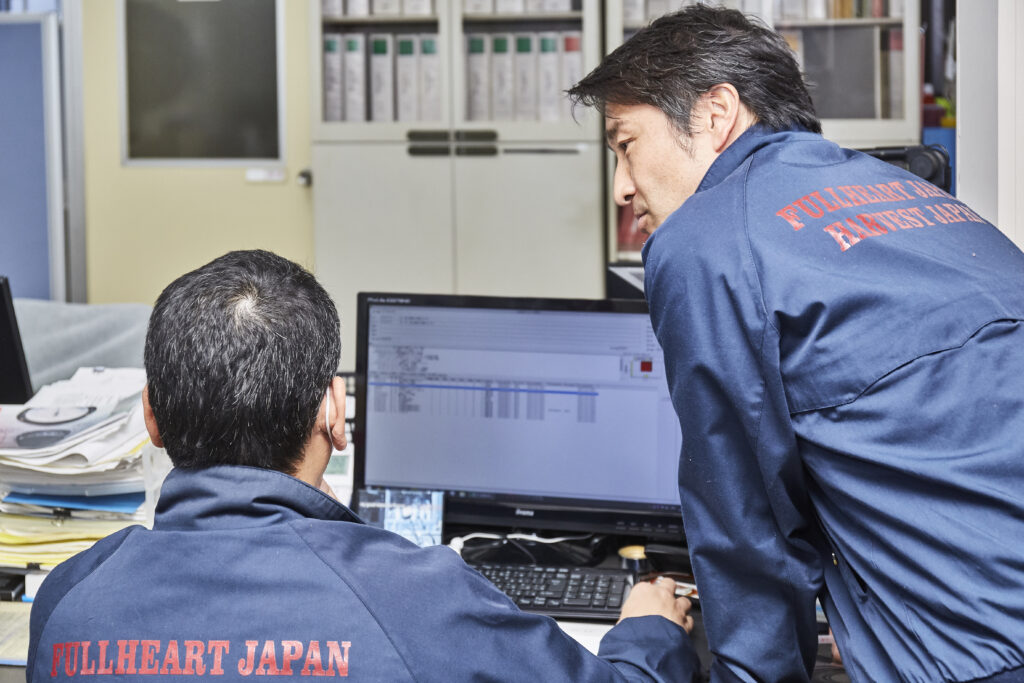
製造業におけるコストダウン設計のポイントは、下記が挙げられます。
- 精度は適切なレベルにする
- 機械設計で部品数を抑える
- 効果を測定して評価する
精度は適切なレベルにする
品質の高い製品を作るためには、精度の高い加工が必要です。しかし、精度の高い加工は、速度の低下や追加工によってコストが高くなります。そのため、必要な部分と不必要な部分を見極めることが重要になります。
必要な部分だけを高精度で加工し、適切なレベルの精度を保つことがコストダウンを考える上で大切です。
機械設計で部品数を抑える
機械設計において、部品数を減らすことで製品のコストを抑えられます。部品が増えると、その部品を製作するコストや組立にかかる時間が増えるため、コストアップは避けられません。
たとえば、ネジをツメに変更するだけでも、組立を容易にし、必要なネジの本数を減らせるなどです。加えて部品数を減らすことは、組立のミスを減らし、製造時間も短くできるのも利点です。
効果を測定して評価する
コストダウン設計を実施する際には、実施前と実施後のコスト比較を行い、効果を測定して評価する必要があります。実施によって製品の品質や性能が低下する可能性がありますし、一部のコストも肥大化するといったことも起きるためです。
コストダウン設計を実施する際には、実施前後の品質や性能の変化を評価し、効果を測定して評価する必要があります。品質や性能を損なうことがないような設計を実施できれば、生産性向上や品質向上なども期待できるでしょう。
【具体例】コストダウン設計における3つの事例
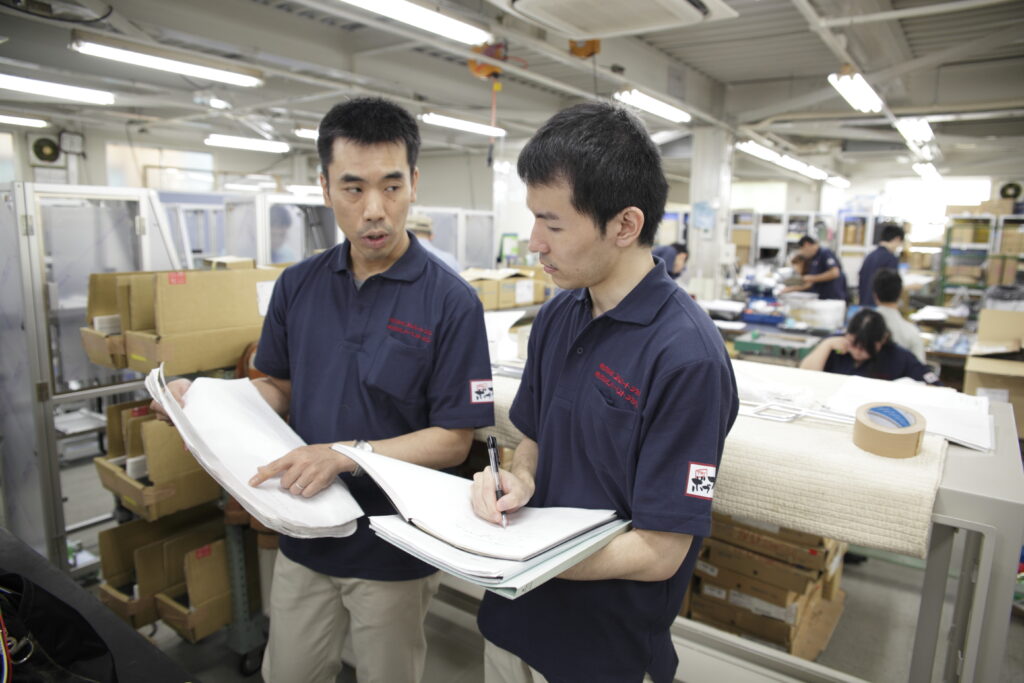
コストダウン設計における3つの事例を下記にわけて紹介します。
- 材料変更によるコストダウン
- 歩留まり解消によるコストダウン
- 作業コストのコストダウン
材料変更によるコストダウン
顧客が推奨した材料と同等性能で、かつ安価で加工が容易な材料を選定しコストダウンした事例があります。焼却装置用の制御盤に使用するヒーターカバーの材料選定時、ヒーターカバーには耐熱性が求められるため、顧客推奨はニッケル合金のインコネルでした。
しかし、インコネルは高価なうえ難削性が高く加工が困難なため、同等性能で安価、また加工性に優れたステンレス(SUS310S)を採用しコストダウンを図りました。
歩留まり解消によるコストダウン
板金の仕様を一工夫することで歩留まりを解消し、コストダウンに成功したケースもあります。安価な部品の場合、取付穴の寸法精度が低いことが多く、組立の際穴位置が合わないことがあります。
フルハートジャパンでは、板金側で部品取付穴を丸穴ではなく長穴にすることで部品の精度が低くても対応可能とし、部品取付時の歩留まり解消に繋がりました。
作業コストのコストダウン
コストダウンは製品に利用する材料コストだけではなく、製造過程にも目を向けた作業工程の見直しも事例として挙げられます。たとえばフルハートジャパンでは、溶接が指定されていた加工部分を溶接よりも短時間で作業ができる曲げ加工に変更。この板金設計により加工時間が大幅に短縮され、作業コスト削減に繋がりました。
作業者が不要な作業を行っていないかを詳細に分析し、無駄な作業を削減したり、作業時間を減らすために自動化や省力化を検討したりすることは重要です。作業コストが大幅に削減され、製品価格の低減にもつながります。
コストダウン設計に関するQ&A
コストダウン設計に関するQ&Aにまとめて回答します。
- なぜ生産設計の見直しが必要なのか
- コストダウンに限界はある?
なぜ生産設計の見直しが必要なのか
コスト削減を目指す企業は、生産設計を見直すことでコストを抑える必要があるためです。そして、そのためには生産設計を定期的にアップデートし続ける必要があります。
技術革新が進む中で、生産設計を見直すことは、新しい技術を取り入れることにもつながります。新しい技術を取り入れられると生産工程も同時に改善でき、生産性の向上を図れるのも利点です。
コストダウンに限界はある?
コストダウン設計は、製品のコストを削減するために有効な手段ですが「限界」があります。材料や部品の品質を下げたり、製造工程を簡略化したりできる一方で、下記のリスクと向きあい続ける必要があるためです。
- 品質の低下
- 開発期間の延長
- 差別化の難化
- 市場の変化
コストダウン設計を行う際には、品質を犠牲にしないようにしたり、開発期間を短縮したりするための工夫を行うなど、慎重な判断が必要です。
まとめ
コストダウン設計においては、初期段階から生産設計を見直すことで、材料変更、歩留まり解消、作業コストの見直しなどが可能です。総合的なコストダウン設計により、トータルコストを下げましょう。
コストダウン設計でお困りでしたら、1968年の創業以来、お客様の「想いと感動」を製品という形に変える「モノづくり」の技術・体制を磨き続けてきた弊社にお任せください。
- 400社以上との取引で培った幅広い業界知識を保有
- 7つの加工技術(設計/開発・組立配線・基板実装・メカトロ組立・計装配管・精密板金加工・塗装)でワンストップサービス
- 経験豊富な技術者でモノづくりをサポート
量産製造にも対応し、電子制御機器の組立・板金加工・塗装処理を得意とする自社工場も完備。高い技術力と生産力でお客様のニーズへしっかりとお応えします。ぜひお気軽にお問い合わせください。